La philosophie du Lean Management
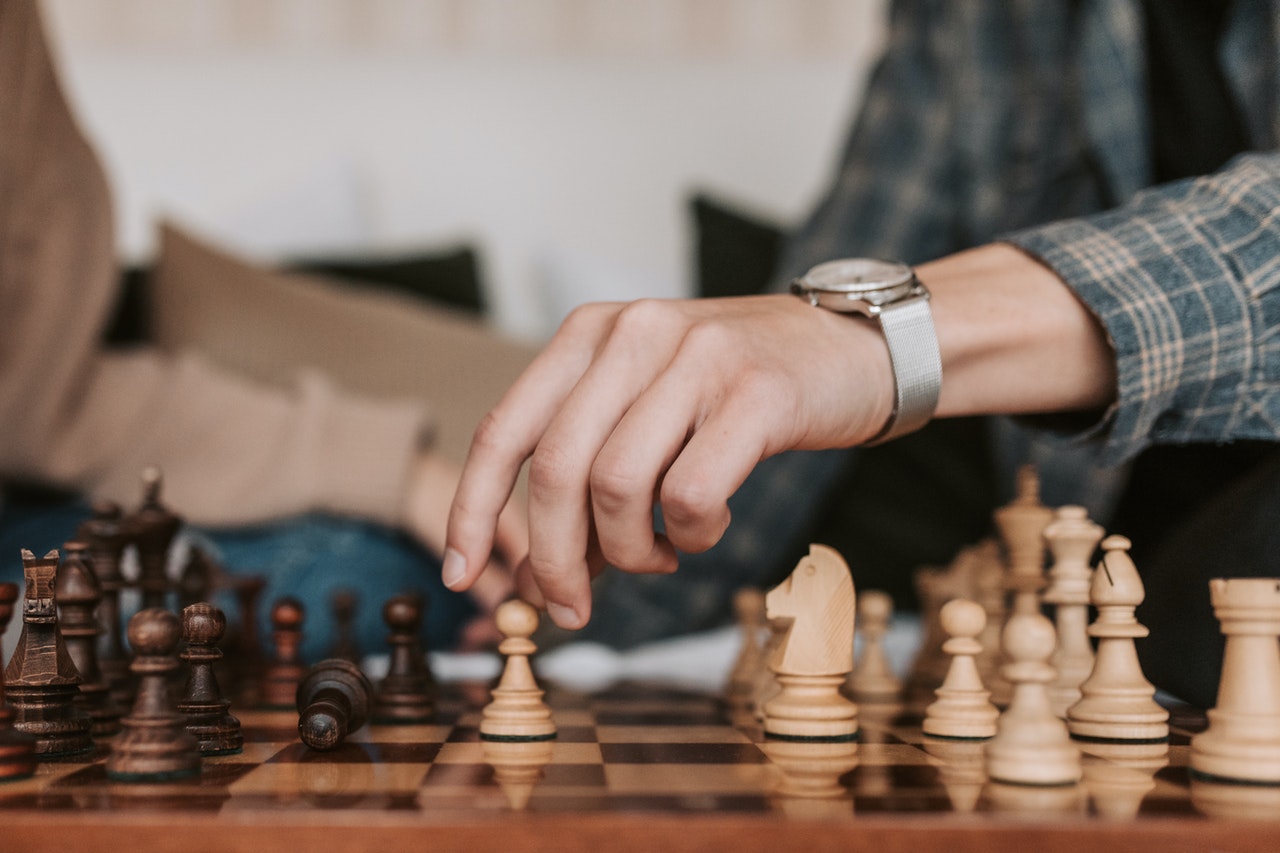
Le Lean est une philosophie de management qui vise à l'amélioration continue en tenant compte du bien être des salariés. Pensée sur le long terme, elle vient satisfaire les attentes du client tout en permettant à l'entreprise d'éviter le gaspillage en matière de production et d'efforts fourni.
Les 8 sources de gaspillage à éviter par la méthode Lean ou Management "maigre" selon Taïchi Ohno, à l'origine du système Toyota :
1. La surproduction
Ne pas produire plus qu'il ne faut. Pour le client c'est un point clé. Créer un stock invendu est une perte de temps d'espace et d'énergie pour les individus impliqués dans la production et une immobilisation de cash. Il faut donc bien prendre en compte tous les paramètres pour dimensionner correctement la taille des lots.
2. Des stocks excessifs
Une grande quantité de stock peut nuire à la production en termes d'espace disponible mais peut également dégrader le working capital. Avoir un stock excessif est souvent synonyme d'une anomalie dans les processus de production. Pour une meilleure productivité il est conseillé d'utiliser tous les moyens des acteurs au bon moment. Cette démarche permet d'éviter le stress et les moments de friction lors d'un projet d'envergure.
3. Eviter les défauts et rebus
En soignant les procédures de production, nous permettons de produire de façon optimisée du premier coup. Cette méthode permet aux acteurs de la production de réduire le temps alloué à la vérification et à la révision des taches à effectuer.
4. Un processus fluidifié
L'amélioration continu des processus de production permet la création d'un cycle de production fluide et ainsi d'éviter les goulots d'étranglement ou passage critique à l'intérieur de processus de production.
5. L'optimisation des moyens d'approvisionnement
L'optimisation des voies et chemins d'approvisionnement permet à la production de gagner en efficacité en évitant la friction de processus contraires ou se ralentissant mutuellement. Les emplacements et lieux de production doivent dont être prêts (libre) et optimisés en prévision d'un besoin urgent.
6. La rationalisation des mouvements
La rationalisation des mouvements permet de prévoir les besoins en terme logistique et d'effort fourni pour atteindre l'objectif. Cette rationalisation vient donc faciliter la prévision des manques en termes d'effort fournit pour atteindre la fin d'un cycle.
7. La suppression des traitements inutiles
La suppression des traitements inutile permet de faire gagner un temps considérable dans le processus global de production. Une manipulation inutile semble dérisoire, mais répétée un grand nombre de fois elle peut faire perdre un temps considérable au bout d'une longue période. Supprimer toutes les actions inutiles, qu'elle soit insignifiante ou non, permet de gagner en efficience et permet de produire plus avec un effort amaigri.
8. La sous-utilisation des compétences
Enfin, la sous-utilisation des compétences, souvent difficile à identifier dans une organisation, représente un gaspillage des ressources des forces de travail mis en œuvre pour atteindre les objectifs.